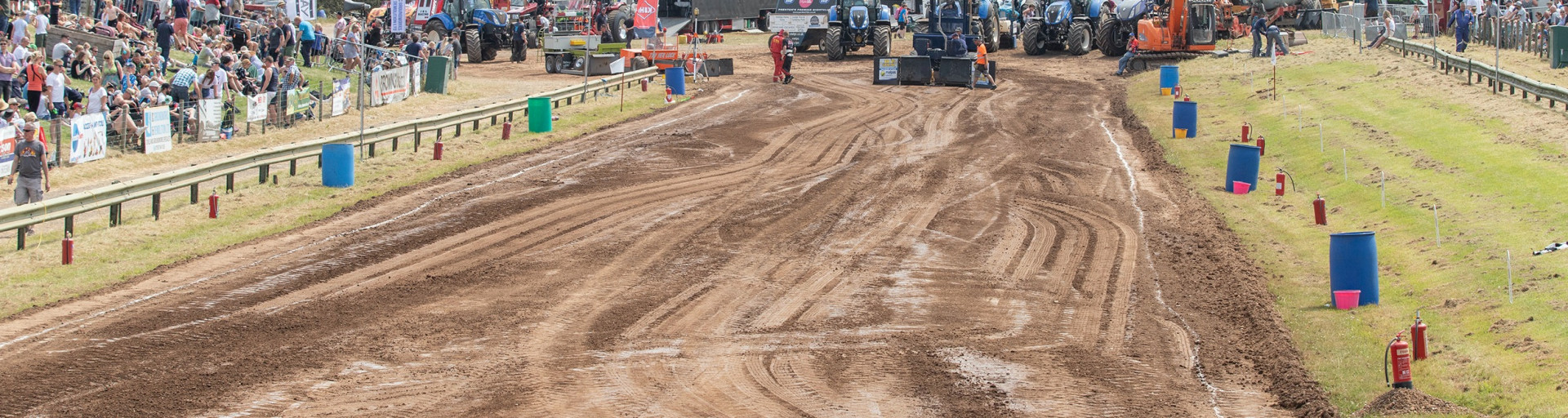
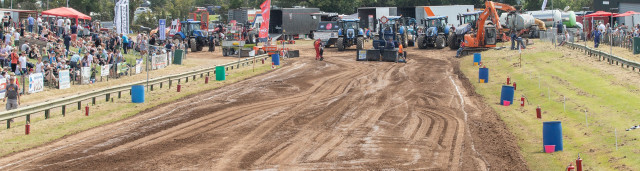
The Track
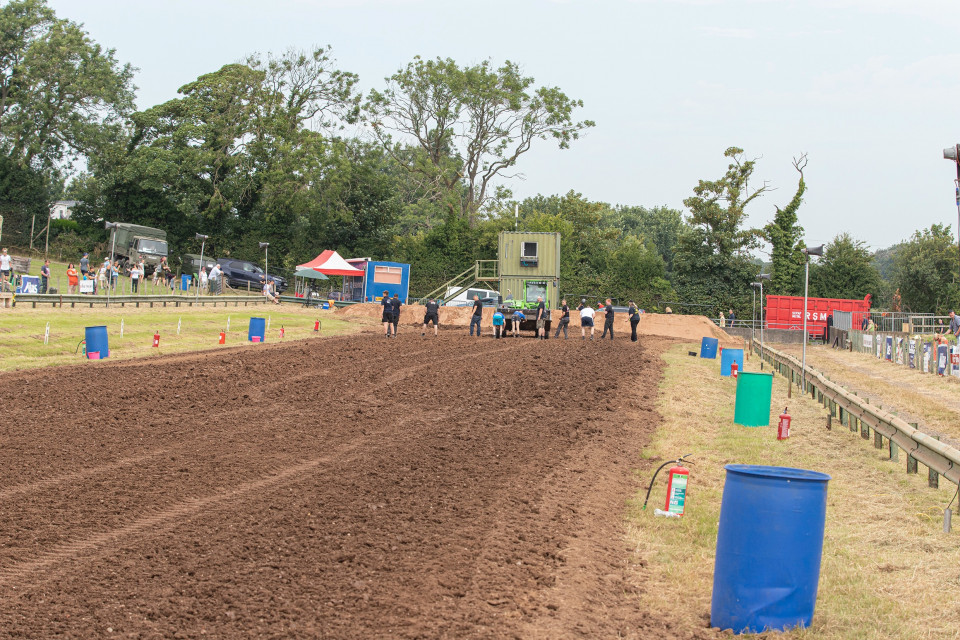
What goes into building a track?
A pulling track comprises dirt. Ideally, the dirt must be free of stones and should include a mix of clay and sand - both have roles to play in contributing to grip and drainage.
UK and European pulling tracks measure 100m in length and no less than 10m wide. A 30m safe run-off area is also required, beyond the finish line. Tracks can have a gradient but only minor. The sub-base should be firm, to hold and carry both the tractor and sledge on the layer of dirt above.
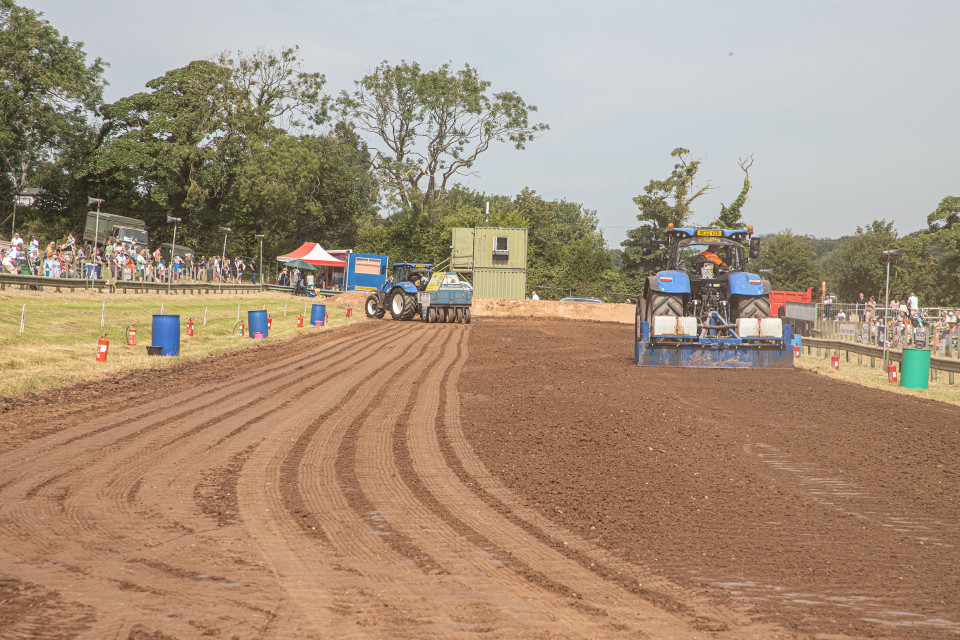
Before the competition starts
Before the start of a day’s pulling, the track surface is opened up and water can be added as necessary to provide a level of moisture that can help hold the track together throughout the day’s competition. After which, the surface is then graded and rolled.
Too much moisture can result in a soft and slippery surface - too little moisture will soon see a track become packed down tight leaving a hard, solid surface that offers no grip. It’s not uncommon for a track to give off heat, after a pounding from a multi-engined modified tractor.
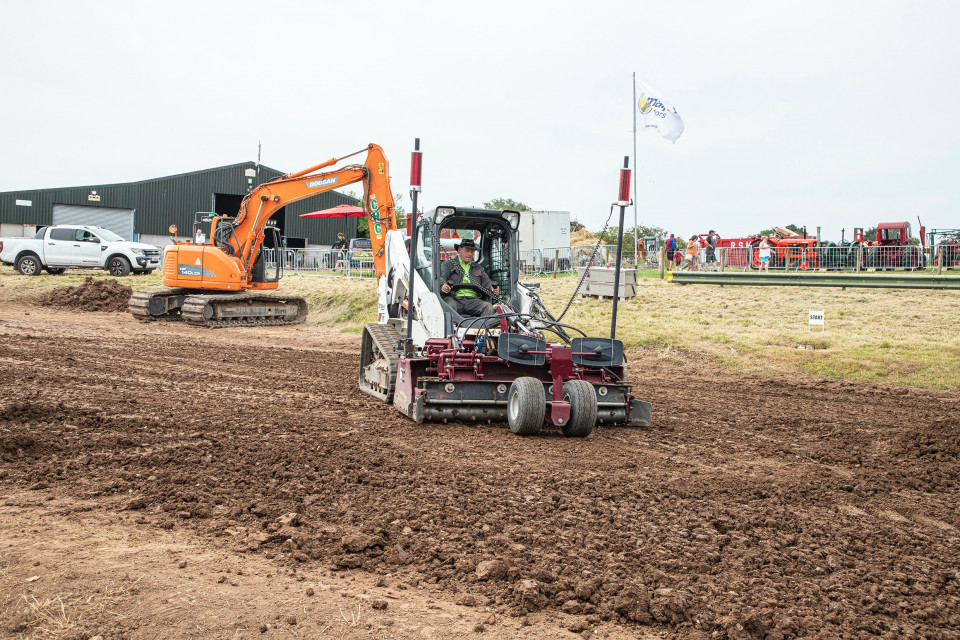
Preparing the start line
It’s important that the sledge sits on a firm, level pad that spans the full width of the track immediately behind the start line. This prevents the sledge from sinking into the surface while it sits waiting for the next tractor to hook.
Every puller has the opportunity to spot the sledge as it comes back to the start line - that is, choose where the sledge sits across the full width of the track. This can be both advantageous and risky as pullers search for maximum grip. Running close to the white line could easily lead to an unwanted disqualification. Brakes are the enemy of speed and no puller wants to use them by choice.
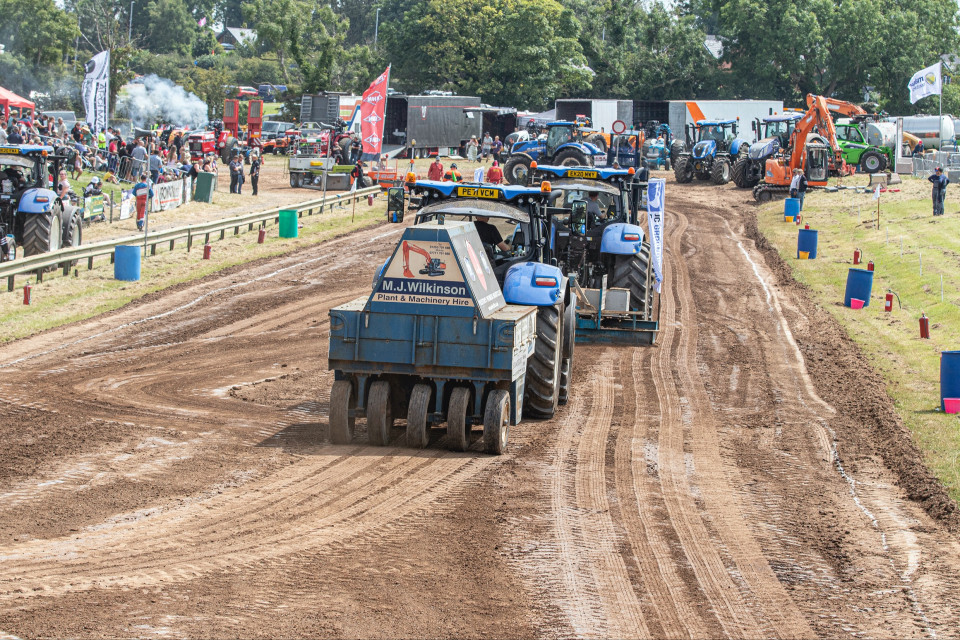
Grading and rolling
After each competitor has pulled, the track is quickly graded and rolled while the sledge returns to the start line. This is to fill holes at the start and level out mounds of dirt thrown in front of the sledge, so that all competitors have a fair and comparable surface on which to pull.
Dirt does get moved around during competition, with most of it getting removed from the start line and dragged along the track. Another reason to carry out quick and immediate remediation.
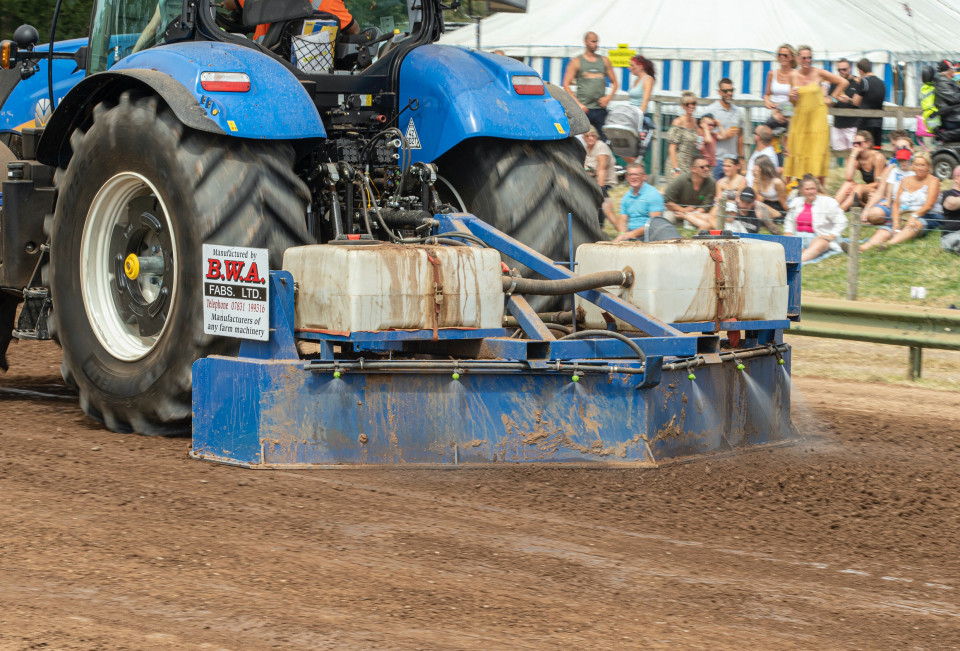
Dust suppression
In addition to grading the track, the crew has the option of simultaneously misting the surface. On a warm day, this is useful to slow the loss of moisture that was put deep into the track at the start of the day. This process can also slow track deterioration that can occur during a big class of powerful tractors.
The running order is randomly drawn - so it’s just a pullers luck whether a track improves or deteriorates during a class. It’s up to the puller to make the most of the surface by spotting the sledge, moving tractor ballast, and altering tyre pressures and hitch height within the rules, when going over the weighbridge.
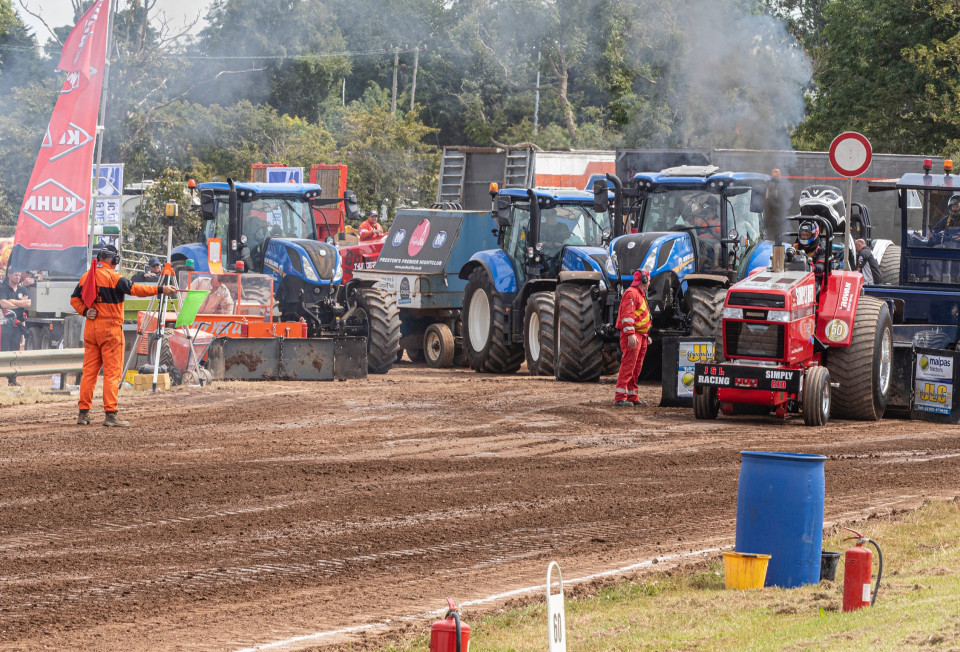
Measuring a pull
Each pull is accurately measured using a laser beam to provide a pull distance to the nearest centimetre. Measurement is taken from a reflective board on the front of the sledge - it’s position on the start line is zero’d, then the total distance travelled by the sledge is measured as soon as the pulling tractor comes to a halt.
Tractors exceeding 100m are considered to have made a Full Pull. When two or more pass the Full Pull line and all competitors have made an attempt to pull in their class, the sledge is made heavier for the pull off. This can be from a combination of techniques including adding weight to the box; topping the box sooner; dropping the back of the pan sooner; or using the pan blades.
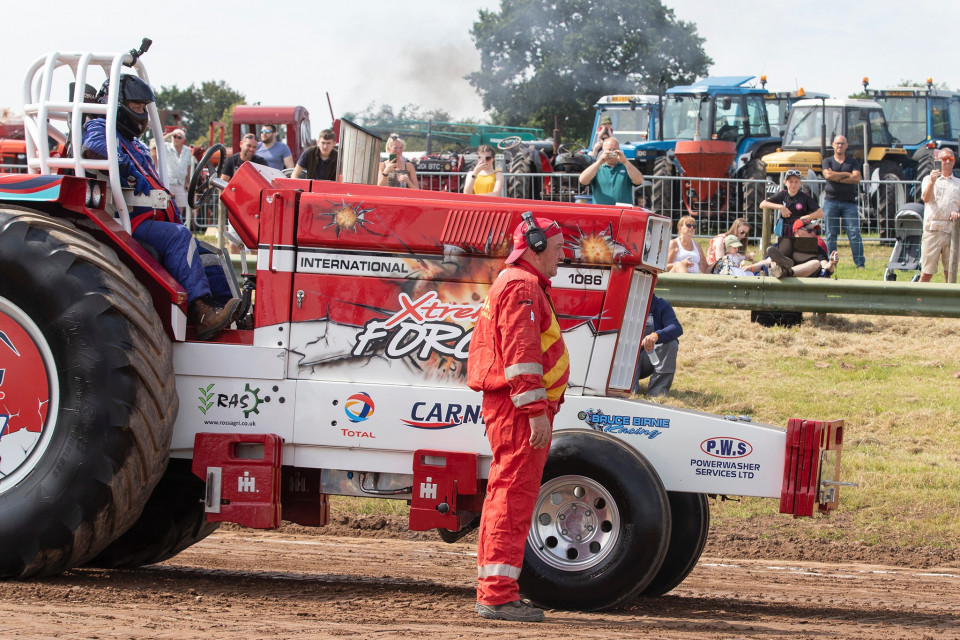
Test puller
The first puller in a class is deemed the test puller. This gives the sledge crew an opportunity to get the sledge setting just right. If it’s too light, there’ll be a pull off that includes almost all the tractors in a class; too heavy and the show will be disappointing as tractors are snuffed out a long way short of the full pull line.
Until the sledge is set, all test pullers are allowed to return six places down the running order. When the sledge is deemed set, the test puller - there could be more than one - has the option of accepting the pull, or dropping six places and returning for a second attempt.
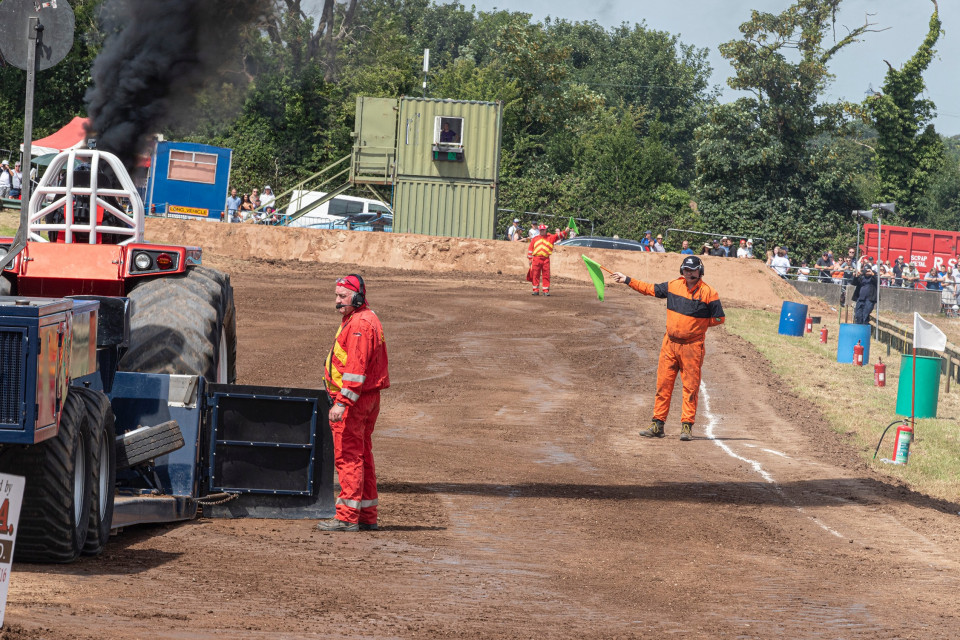
Throttling off
When a puller leaves the line there is one immediate opportunity to regroup if there’s doubt over tractor performance, gear choice, or simply not enough rpm to get away. And many can nervously leave the line too soon before the tractor is fully alive. So the competitor can throttle-off and make an immediate second attempt.
This is only allowed if the tractor comes to a controlled stop before the 30m-mark, where white track-side flags serve as a reminder to either back out or keep going. The sledge is moved back to the start line, pulling the tractor back with it. And in this instance, no further track preparation is allowed.
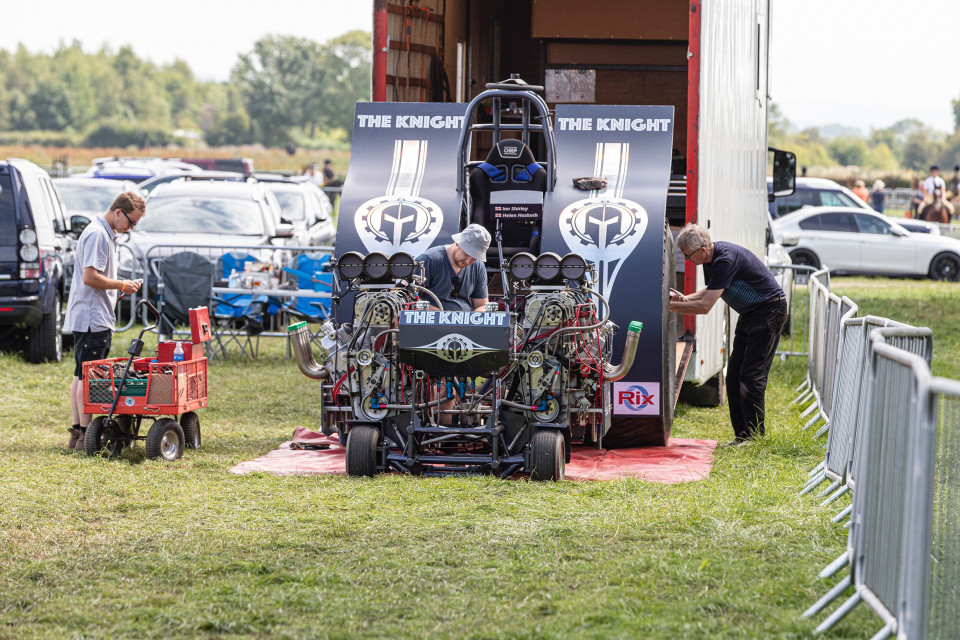
Getting ready
Before tractors are towed to the closed pit area, final checks and adjustments are made. Tyre pressures are lowered from their transport pressures, weights are usually added or removed, cameras can be fitted for extra data recording, and fuel tanks topped-up.
Pulses quicken, hearts start racing and pressure builds. This is not a time for distractions and everything must be right. When a tractor is called to the sledge, the clock counts down, so everyone must be strapped in and ready to go - a puller has just three minutes to hitch to the sledge and pull, otherwise disqualification awaits. Technical problems do arise, and communication with the head track marshall is then essential.
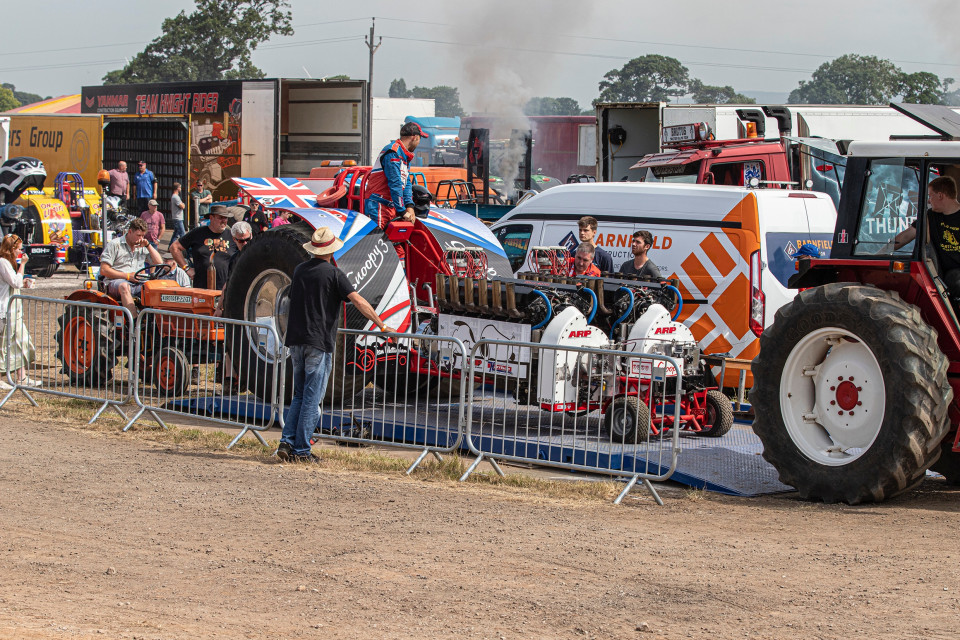
Weighing up
Before each tractor reaches the track, all must pass over a weighbridge en-route to the closed pit area. Tractor with full fuel tanks, driver complete with firesuit and helmet, must not exceed the maximum weight allowed for that class. At the same time, drawbar height is measured - this can be up to a maximum of 50cm from the ground.
Once in the closed pit area, kill switches are tested and confirmed using a coloured tie-wrap. If the kill switch is activated during a pull, a broken tie-wrap proves the function.